From the RTB 2015 Annual Report
Much of the cassava grown in developing countries is processed to produce starch or flour used as ingredients in an array of food products. As demand for those products grows, the cassava processing industry will play an increasingly important role for farmers and local economies. The CGIAR Research Program on Roots, Tubers and Bananas (RTB) has consequently supported research to help starch and flour producers become more efficient.
In many countries, processing is primarily done by small- and medium-scale operations, which frequently suffer inefficiencies – particularly in energy use – that negatively affect their profitability and the environment. A cross-center team of researchers studied cassava processing operations in several countries to identify problems and measures that could be taken to correct them. Their research resulted in guidelines to improve the efficiency of small- and medium-sized processing enterprises, which can in turn ensure higher, stable prices for the smallholders who supply them.
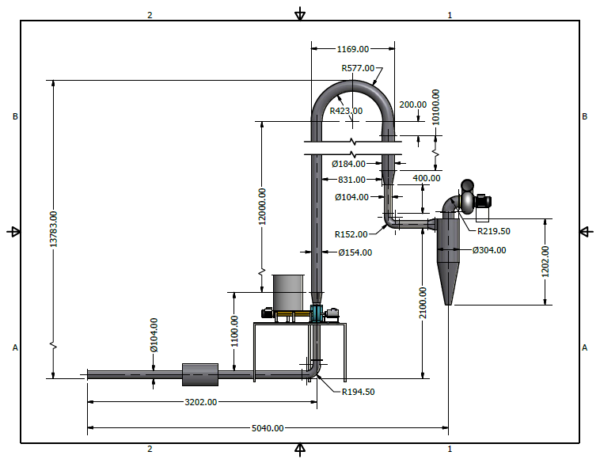
Sample plan for energy efficient flash dryer for cassava. Credit: Francisco Javier Giraldo Cuero (Univalle), Arnaud Chapuis (CIRAD), Martin Alonso Moreno Santander (Univalle), Dominque Dufour (CIAT, CIRAD), Thierry Tran (CIRAD).
The study was conducted by a team of researchers from the International Center for Tropical Agriculture (CIAT), CIRAD and the International Institute of Tropical Agriculture (IITA), with support from Univalle and Clayuca in Colombia, Kasetsart University and KMUTT in Thailand, and Thai Nguyen University in Vietnam. The cooperation of industrial partners such as Niji Lukas (Nigeria), Ukaya Farms (Tanzania), Almidones de Sucre (Colombia), CODIPSA (Paraguay) was also essential.
The team determined that because artificial drying is faster than sun drying, it can be a key factor for increasing production capacity. However, artificial drying consumes 70%-75% of the total energy used by a typical cassava starch/flour factory, which means that inefficiencies in the drying process can significantly increase production costs. They determined that ‘flash drying’ is one of the most suitable technologies for the production of cassava starch or flour, and that large-scale flash dryers (200-300 tons of product/day) are highly energy efficient. However, on a small scale (< 50 tons of product/day), flash-dryer energy efficiency is only 40-60%, due to inadequate dryer designs.
The researchers developed a numerical model to simulate flash drying at both small and large scales and investigated ways to improve energy efficiency. Using computer simulations coupled with multi-objective optimization methods, they determined the optimal flash dryer dimensions and operating conditions for different production capacities. They then developed guidelines for the design of energy-efficient flash dryers.
Those guidelines and research findings were shared with key stakeholders from the private and public sector at a workshop in Bangkok, Thailand in December 2015. Workshop participants included representatives of cassava processing factories, equipment manufacturers, universities and government agencies from Thailand, Vietnam, Myanmar, Indonesia, Philippines, Colombia, Nigeria, Tanzania, France and Germany.
Engineers at the Colombian university Univalle are using the guidelines to produce blueprints for an energy-efficient, small-scale flash dryer, a prototype of which is slated to be built in 2016. Other organizations in Indonesia, Myanmar and South Africa have also expressed interest in energy-efficient, small-scale flash dryers. The researchers will continue to share their findings at events in Africa and Latin America.